In this article
To survive in today’s highly competitive market, food and beverage manufacturers need to be able to compete on price, quality and sustainability.
This means a company’s systems and processes need to be not only failsafe, but streamlined to keep costs down, and flexible to meet changing industry or consumer requirements.
Pie in the sky? Happily, it’s not. With the right software solution, you can grow and scale your business while keeping your costs low and upholding the highest level of quality control.
Find out what an enterprise resource planning system (ERP) can do for you, and if it’s time to upgrade to one.
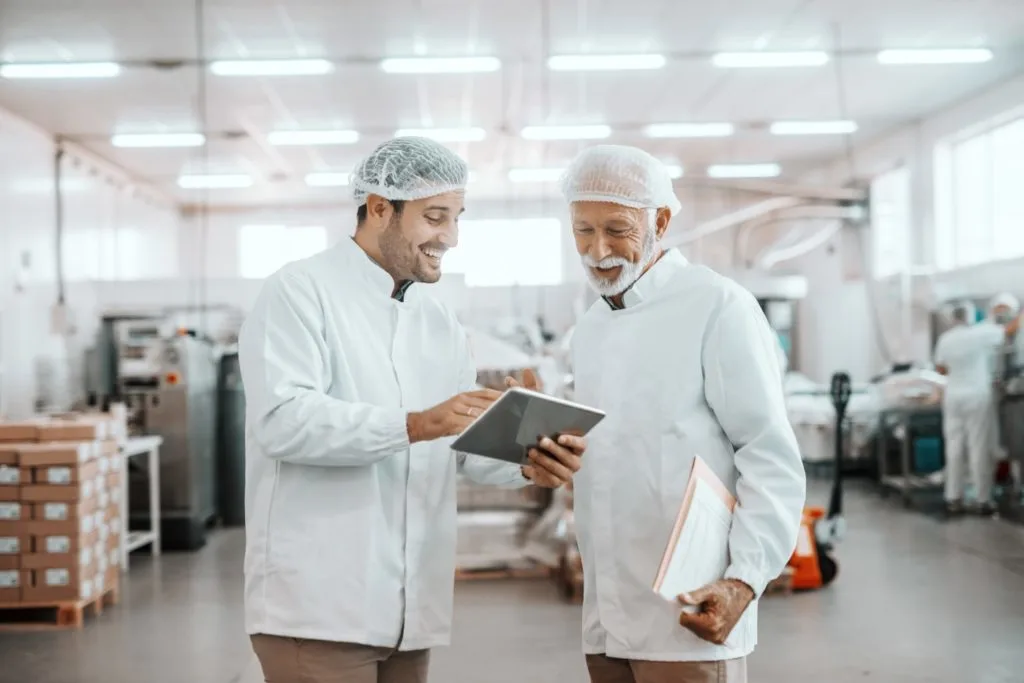
Digital disconnection: a handbrake on growth
Many small and medium-sized food and beverage manufacturers run their business off basic accounting software, Excel spreadsheets and a range of other software applications that may not ‘talk’ to each other.
Read: Connec Operations – Ready for market leadership
Inevitably this digital disconnection becomes a handbrake on growth.
If you want to increase your volumes, for example, the administrative work that you need to do to support this becomes increasingly onerous and prone to error.
Without systems integration, there’s little visibility or control over the end-to-end manufacturing process — and when you’re operating in the dark, things can (and do) go wrong, and costs blow out.
What does this mean for small and mid-sized manufacturers?
What’s clear is that to remain relevant and competitive amid pervasive change, food and beverage manufacturers need to tackle digital disconnection and reduce their time to market.
For many businesses, the best way to achieve this is to upgrade their company software to a cloud enterprise resource planning (ERP) platform.
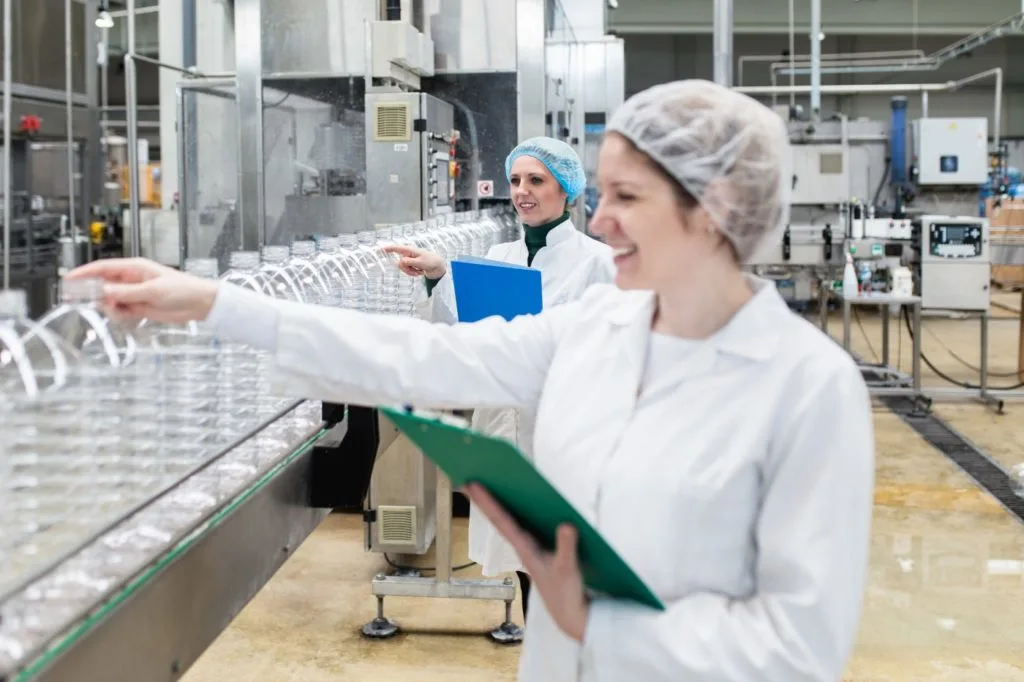
What is an ERP?
An ERP platform is an integrated business management software suite that connects company-wide data, systems and processes and brings them together in one database to provide a holistic view of the business.
The platform’s seamless integration between applications means data flows freely through the system.
This reduces the need for manual data entry and cross-checking between systems, saving time and decreasing the potential for errors. This data flow also enables process automation, increasing efficiency and helping to lower operational costs.
As a business management tool, a cloud ERP such as MYOB Acumatica Manufacturing provides visibility across all areas of the business in real-time.
With all the latest company information at their fingertips, the management team is empowered to make better decisions and create business value.
At the click of a button, management can visualise results, track progress, and see the impact of changes made.
How do you know when you’re ready for a cloud ERP?
The right time to move to an ERP platform is when you decide you’re ready to invest in software to take your business to the next level.
Perhaps you’re growing rapidly — or perhaps you have ambitions to do so and recognise you’re held back by relying on accounting software, spreadsheets and manual processes.
The reality is that when companies continue to rely on legacy systems and processes when undergoing rapid growth or navigating industry change, they put their people under tremendous stress.
Here are some key indications it may be time to upgrade to an ERP:
Inefficiency
You’re entering data manually into multiple systems and cross-checking updates between them. You’re losing sales due to internal errors, re-work, and the time it takes to go to market.
Document management
You may have intellectual property — such as recipes — saved in multiple spreadsheets. Keeping track of changes and maintaining data integrity may be problematic.
Compliance
You need to find workarounds to comply with new regulatory or reporting requirements. You don’t have complete confidence in your quality control, traceability and recall mechanisms.
Visibility
It’s impossible to get a comprehensive view of the business. This makes production scheduling very challenging. It also makes it too difficult to scale your business, add product lines or new sales channels.
Reporting
Your reports contain errors and may be out of date. It’s hard to make informed decisions without complete data at every stage of the production process.
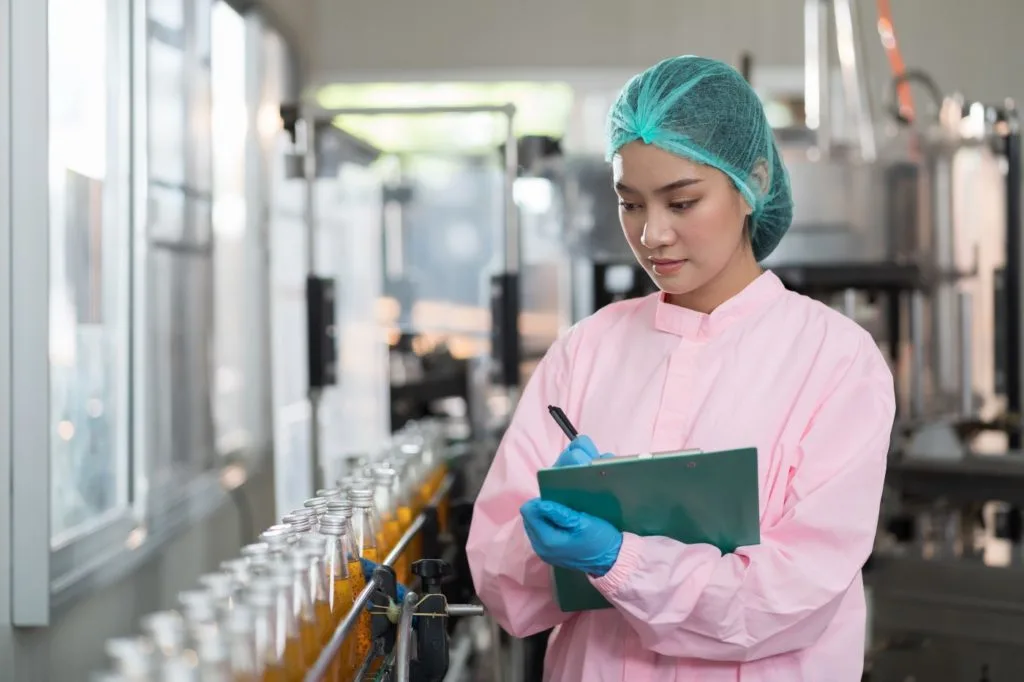
What business benefits does an ERP provide?
By bringing all your company information together in one inter-connected system, an ERP helps you streamline your operations, remove costly inefficiencies, future-proof your software, and increase sales and profitability.
The benefits of a modern, cloud ERP include accessibility, easy integration with other cloud-based solutions, increased operational efficiency, automated processes, real-time data and reporting and analytical tools to evaluate that data, and consolidated financial reporting across multiple entities.
An ERP can also assist with many of the most common food and beverage manufacturing challenges, including:
Formula and recipe management
Compliance
Quality control
Production control
Batch management
Tracking and traceability
The last dot point is particularly important, as the cost of not having an effective track-and-trace system can be significant.
A recent example in Australia was when a significant amount of fruit was recalled after needles were found in strawberries, bananas and apples. This caused widespread safety concerns and significant nationwide economic damage to fruit producers.
An ERP with track and trace functionality allows food and beverage manufacturers to generate product recall notices through the system, swiftly notifying affected customers and distributors of any quality control issues.
The ability to track products by lot or serial number — from production to point of sale — can give all stakeholders assurance that you have robust systems and processes in place to uphold public safety.
As a result, customers can continue to purchase from you across all product lines with confidence.
What does MYOB Acumatica Manufacturing offer?
MYOB Acumatica Manufacturing is a cloud ERP that offers food and beverage manufacturers a complete and integrated quality solution so you can have confidence in your control measures at every stage of the production process.
Further, with all your quality control information captured in one place, you have a full audit trail and the visibility to quickly respond to any issues.
You can also easily generate reports, enforce accountability for quality-related actions, and automate workflows to increase efficiency and reduce time to market.
The next move to maximise your manufacturing efficiency
In today’s market, digitisation is a must.
As a company grows, it becomes increasingly important to move away from paper-based processes, which become exponentially more chaotic and inefficient.
Ultimately, ineffective systems and processes also affect customer service, sales, and profitability.
By bringing all key business information together, a company can benefit from best practice processes, increase operational efficiency, reduce costs, and gain better visibility and control.
Deploying an ERP modernises a business and helps it remain competitive in an increasingly fast-paced economy.
It also future-proofs IT systems by providing a platform that can integrate additional third-party applications down the track.
MYOB Acumatica Manufacturing is designed for mid-sized companies like yours. And with its connected workflows and strong quality capability, it’s the perfect choice for food and beverage manufacturers.
Information provided in this article is of a general nature and does not consider your personal situation. It does not constitute legal, financial, or other professional advice and should not be relied upon as a statement of law, policy or advice. You should consider whether this information is appropriate to your needs and, if necessary, seek independent advice. This information is only accurate at the time of publication. Although every effort has been made to verify the accuracy of the information contained on this webpage, MYOB disclaims, to the extent permitted by law, all liability for the information contained on this webpage or any loss or damage suffered by any person directly or indirectly through relying on this information.